Comprehensive Guide to h2s monitor calibration and Its Impact on Business Success
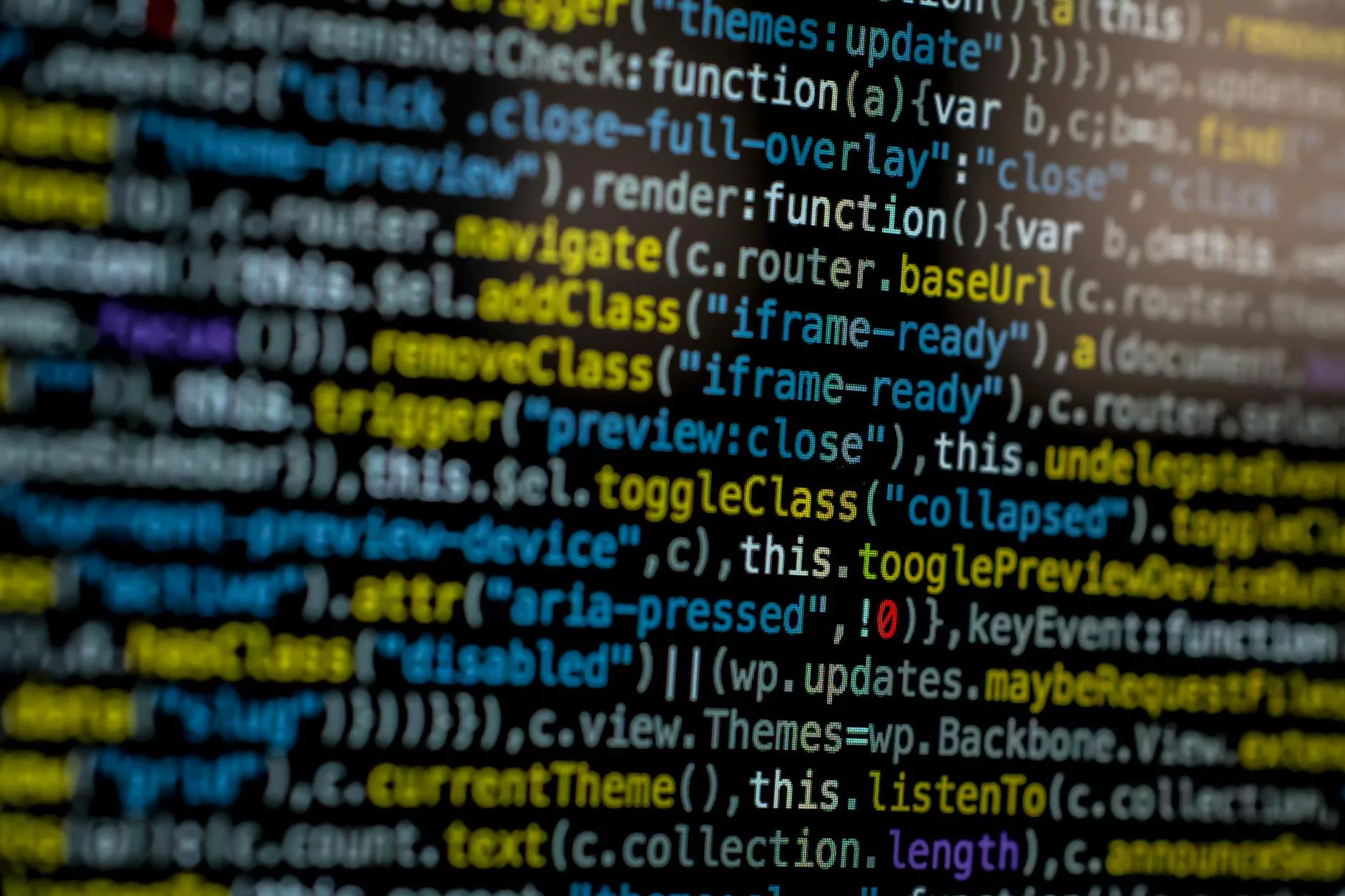
In today's rapidly evolving industrial and educational landscapes, precision and safety are more critical than ever. One of the fundamental components ensuring both are h2s (hydrogen sulfide) monitor calibration. Whether you operate within the realm of Educational Services or Special Education, maintaining accurate hydrogen sulfide detection is paramount for creating safe, compliant, and efficient environments.
Understanding the Significance of h2s monitor calibration
The calibration of H2S monitors is a technical process designed to ensure these devices provide accurate readings of hydrogen sulfide gas concentrations. Hydrogen sulfide is a toxic and flammable gas, often encountered in industrial settings, wastewater treatment, and certain educational laboratories. Accurate detection can prevent occupational hazards, protect human health, and avert costly accidents.
In educational and special education settings, remotely monitoring gas levels or training on safety protocols necessitates reliable detection equipment. Proper h2s monitor calibration ensures that educators, students, and staff can confidently identify hazards and respond appropriately.
Why h2s monitor calibration is Critical for Businesses in Educational Services
Educational institutions, especially those involved in vocational training or laboratory sciences, often utilize gas detection devices as part of their safety infrastructure. Regular h2s monitor calibration guarantees that these devices perform reliably, fostering a secure learning environment.
- Ensures Accurate Readings: Precise calibration prevents false alarms and undetected hazards.
- Supports Regulatory Compliance: Many jurisdictions mandate regular calibration to meet occupational safety standards.
- Enhances Safety: Accurate detection mitigates risks associated with hydrogen sulfide exposure.
- Reduces Costs: Properly calibrated monitors reduce false alarms, maintenance costs, and potential liability.
- Builds Trust: Reliable safety measures increase confidence among staff, students, and regulatory bodies.
Challenges in Maintaining h2s monitor calibration
While calibration is vital, it comes with challenges, especially in the context of educational and specialized environments:
- Calibration Frequency: Determining the optimal interval between calibrations to maintain accuracy without unnecessary costs.
- Technical Expertise: Requiring trained personnel or certified services for proper calibration.
- Environmental Factors: Temperature, humidity, and exposure to other chemicals may affect monitor performance and calibration stability.
- Device Age and Wear: Older devices may drift from original calibration settings, necessitating more frequent adjustments.
- Cost Implications: Regular calibration and maintenance incur expenses that need budgeting and planning.
Best Practices for h2s monitor calibration to Optimize Business Operations
Implementing best practices ensures your organization maintains high safety standards while minimizing downtime and costs. Here are recommended strategies:
1. Use Certified Calibration Sources
Always calibrate H2S monitors using certified calibration gases that meet industry standards. These gases provide known concentrations of hydrogen sulfide and serve as benchmarks for accurate device calibration.
2. Follow Manufacturer Guidelines
Adhere strictly to the calibration procedures specified by the device manufacturer. Each sensor type may have unique calibration requirements, and neglecting these can lead to inaccuracies.
3. Maintain a Regular Calibration Schedule
Establish a routine calibration timetable—commonly every 3 to 6 months—based on usage frequency and environmental factors. Document every calibration activity for compliance and quality assurance.
4. Train Staff and Technicians
Ensure personnel responsible for calibration are properly trained. Certification courses and hands-on training improve calibration quality and reliability.
5. Perform Pre- and Post-Calibration Checks
Before calibration, verify the monitor’s baseline functionality. After calibration, test the device with known gas concentrations to confirm calibration accuracy.
6. Use Maintenance and Diagnostic Tools
Utilize advanced diagnostic tools to detect sensor drift, sensor aging, or potential malfunctions, ensuring ongoing reliability of your monitors.
Advanced Technologies in h2s monitor calibration
As technology advances, calibration methods now include automated calibration systems that simplify and improve accuracy. These integrated systems can calibrate with minimal human intervention, reduce errors, and generate real-time calibration reports, streamlining process management for educational and industrial settings.
Moreover, digital calibration devices can interface with your existing monitors, providing precise adjustments and detailed diagnostics. Utilizing such technologies helps ensure continuous compliance, safety, and operational readiness.
The Role of Professional Calibration Services in Ensuring Safety and Accuracy
While many organizations opt for in-house calibration, engaging professional calibration services offers several advantages:
- Expertise and Experience: Certified technicians possess extensive knowledge of calibration standards and gas detection systems.
- Compliance Assurance: Professional calibrations adhere to national and international safety standards, aiding in regulatory compliance.
- Time and Cost Efficiency: Outsourcing calibration reduces downtime, minimizes operational disruptions, and guarantees accurate results.
- Enhanced Calibration Precision: State-of-the-art equipment and controlled environments lead to superior calibration accuracy.
For educational institutions and facilities involved in special education, where safety is non-negotiable, partnering with reputable calibration providers ensures continuous reliable detection of hydrogen sulfide and other hazardous gases.
Integrating Calibration and Safety Protocols in Business Operations
Calibration should be integrated into your organization's comprehensive safety management system. Regular audits, staff training, and calibration recordkeeping form a robust safety culture that prioritizes health and compliance.
Furthermore, programs should include periodic risk assessments and emergency response drills to reinforce proper reactions to hazardous gas readings, ensuring everyone understands and adheres to safety protocols.
Importance of Ongoing Education and Training
Staying updated with the latest calibration technology, safety standards, and regulatory requirements is crucial. Continuous education ensures that staff and technicians can effectively manage calibration processes and respond to new challenges.
Educational services offered by h2sonlinetraining.com provide specialized courses focusing on gas detection, calibration procedures, safety management, and compliance, empowering your team with essential skills.
Conclusion: Investing in Proper h2s monitor calibration for Business Excellence
In conclusion, the importance of h2s monitor calibration cannot be overstated in creating safe, compliant, and efficient environments within both educational and industrial sectors. Accurate calibration ensures reliable detection, reduces operational costs, and supports regulatory adherence, ultimately safeguarding human health and your organization’s reputation.
By adopting best practices, leveraging advanced technologies, and engaging professional calibration services, your business can maintain the highest standards of safety and operational excellence. Invest in proper calibration protocols today and demonstrate your commitment to safety, compliance, and continuous improvement.