Understanding Industrial Blade Manufacturing
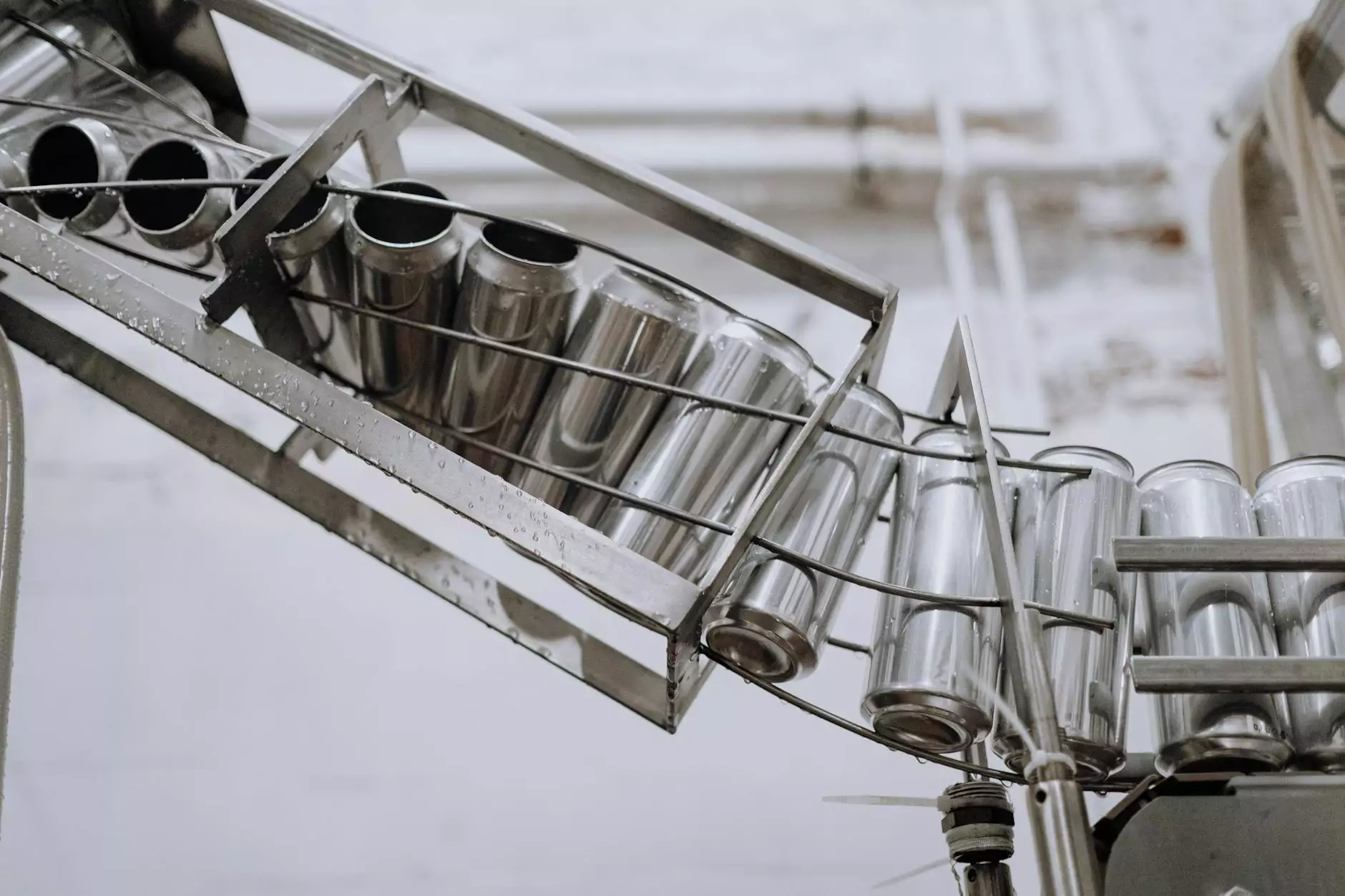
Industrial blade manufacturing plays a pivotal role in various industries requiring cutting tools that are not only precision-engineered but also durable and reliable. From woodworking to metal processing, the correct choice of blades significantly impacts operational efficiency, product quality, and overall cost-effectiveness.
The Significance of Industrial Blades
Blades used in industrial applications are specialized tools designed for cutting, slicing, and shaping various materials. The significance of these blades includes:
- Precision: Industrial blades are engineered to achieve high levels of precision, ensuring clean cuts that minimize waste and maximize usability.
- Durability: Built from high-grade materials, industrial blades are designed to withstand heavy use without compromising their integrity.
- Cost Efficiency: Investing in quality blades reduces replacements and maintenance, leading to long-term savings.
- Customization: Many manufacturers offer customized blade solutions tailored to the specific needs of various industries.
Key Components of Industrial Blade Manufacturing
The process of industrial blade manufacturing involves various critical steps that ensure the highest quality and performance of blades. Understanding these components can help businesses make informed decisions when sourcing their cutting tools.
Material Selection
The choice of material is paramount in blade performance. Common materials used in blade manufacturing include:
- High-Speed Steel (HSS): Excellent for cutting tools due to its toughness and ability to retain sharpness.
- Carbide: Known for its hardness and wear resistance, ideal for high-speed applications.
- Stainless Steel: Corrosion-resistant and suitable for applications in moist environments.
- High Carbon Steel: Exceptional edge retention and toughness make it suitable for various cutting applications.
Manufacturing Processes
Manufacturing industrial blades often involves several sophisticated processes, including:
- Forging: Creates a strong structure through the application of heat and pressure.
- Grinding: Ensures precise dimensions and sharp edges.
- Coating: Enhances performance by providing additional protection against wear, corrosion, and adhesion.
- Heat Treatment: Alters the physical properties to increase the blade's strength and durability.
Quality Control
Quality assurance is an integral part of manufacturing industrial blades. Manufacturers conduct rigorous testing for:
- Dimensional Accuracy: Ensures that the blades meet specified size and tolerance requirements.
- Tensile Strength: Evaluates the blade's ability to withstand forces without breaking.
- Sharpness Tests: Verifies the edge's effectiveness in cutting applications.
Applications of Industrial Blades
Industrial blades have a wide array of applications across multiple sectors. Here are some sectors where they play a crucial role:
- Woodworking: Used in saw blades and planers to achieve accurate cuts and finishes.
- Metal Fabrication: Essential in cutting tools like shears and saws for metals.
- Food Processing: Employed in slicing and dicing machines for efficiency and hygiene.
- Textiles: Blade cutting machines expedite the process of fabric production and handling.
Professional Services in Blade Maintenance
A crucial aspect of ensuring the longevity and performance of industrial blades is regular maintenance. Knife sharpening is one of the professional services that should not be overlooked. Understanding why this service is important can add value to your business operations.
Why Knife Sharpening Matters
Regular knife sharpening services yield numerous benefits, including:
- Improved Performance: Sharp blades cut more efficiently, reducing operational strain.
- Increased Safety: Dull blades can slip or require additional force, leading to accidents.
- Cost Reduction: Timely sharpening can extend the lifespan of blades, reducing replacement costs.
How Professional Sharpening Works
Professional knife sharpening involves a systematic approach to revive blade sharpness:
- Assessment: Technicians evaluate the blade's condition to determine the appropriate sharpening technique.
- Sharpening: Various methods such as grinding or honing are used based on blade material and design.
- Finishing: Polishing the edge ensures a fine, sharp surface conducive to optimal cutting performance.
Choosing the Right Industrial Blade Manufacturer
When selecting an industrial blade manufacturing partner, several factors should be considered:
- Reputation: Research the manufacturer’s market standing and customer reviews.
- Expertise: Choose a company with extensive experience in your specific industry.
- Customization: Your manufacturer should offer tailored solutions to meet your unique requirements.
- Customer Support: Reliable customer service is essential for addressing inquiries and maintenance needs.
The Future of Industrial Blade Manufacturing
As industries advance, so too does blade manufacturing technology. Emerging trends include:
- Smart Manufacturing: Integrating IoT technology for real-time monitoring of blade performance.
- Advanced Materials: Research into new composite materials that offer enhanced durability without added weight.
- Environmental Considerations: Focus on eco-friendly manufacturing processes and recycling of old blades.
Conclusion
In conclusion, industrial blade manufacturing is a cornerstone of many industries, significantly influencing productivity and safety. As companies look for ways to enhance their operational efficiency, understanding the details of blade manufacturing and maintenance, including services like knife sharpening, is essential. By selecting the right manufacturing partner and prioritizing blade care, businesses can ensure superior quality and longevity in their cutting tools.
For businesses looking to make informed decisions about blade sourcing and maintenance, explore the offerings at SZBlade.com. With professional services and a commitment to quality, you can take your operations to the next level.