Comprehensive Guide on Lathe Turning Parts Manufacturers
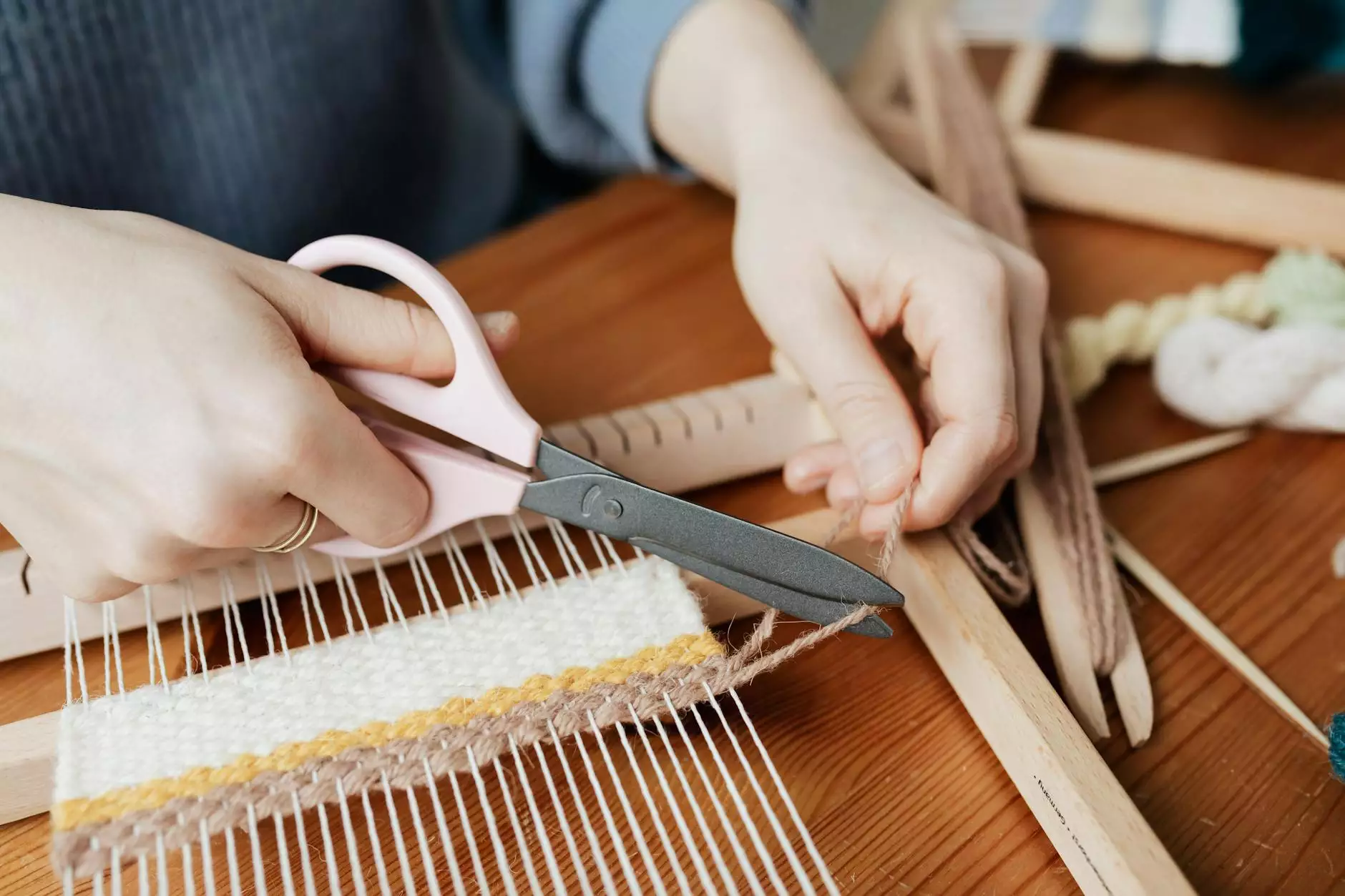
Lathe turning parts manufacturers play a crucial role in the metal fabrication industry, contributing to a host of applications from automotive to aerospace. Understanding their importance, processes, and innovations enables businesses and consumers to appreciate the craftsmanship that goes into creating finely-tuned machine components. In this article, we’ll explore the intricacies of lathe turning, highlight the features of reputable manufacturers like Deep Mould, and discuss the benefits they bring to various industries.
What is Lathe Turning?
Lathe turning is a subtractive manufacturing process that involves rotating a piece of material—in most cases, metal—against a cutting tool to produce a desired shape and finish. This technique is pivotal in creating cylindrical parts and is used extensively in various applications.
History of Lathe Turning
The history of lathe turning dates back to ancient Egypt, where simple wooden lathes were utilized. Over the centuries, advancements in technology led to the development of metal lathes, which significantly enhanced the precision and versatility of the turning process. Today, modern lathes are equipped with advanced computer numerical control (CNC) technology, allowing for unparalleled accuracy and efficiency.
The Role of Lathe Turning Parts Manufacturers
Lathe turning parts manufacturers are integral to industries that require high-quality components. These manufacturers provide a variety of services, including:
- Custom Machining: Tailored solutions to meet specific client needs.
- Mass Production: Efficiently producing large quantities of parts while maintaining quality.
- Prototyping: Creating prototypes for testing and development purposes.
- Precision Engineering: Utilizing advanced tools and techniques to ensure exact specifications.
Industries That Benefit from Lathe Turning Parts
Many industries require parts manufactured through lathe turning, including:
- Aerospace: Components used in aircraft and spacecraft.
- Automotive: Parts for engines, transmissions, and body structures.
- Medical Devices: Precision instruments and devices.
- Electronics: Components for consumer and industrial electronics.
Key Benefits of Working with Reputable Manufacturers
When collaborating with respected lathe turning parts manufacturers, businesses gain several advantages:
- Quality Assurance: High standards are maintained throughout the manufacturing process, ensuring product reliability.
- Expertise and Experience: Skilled engineers and machinists bring years of experience and knowledge to each project.
- Advanced Technology: State-of-the-art equipment and software lead to superior product quality.
- Competitive Pricing: Efficient manufacturing processes help to keep costs down.
Technology in Lathe Turning
Modern lathe turning incorporates various technologies that improve efficiency and precision. Some notable advancements include:
CNC Machining
CNC (Computer Numerical Control) machining allows manufacturers to program exact specifications into the machine, ensuring precision and consistency across all parts produced. CNC lathes can execute complex designs that would be incredibly tedious or impossible to achieve manually.
Automation
Automation in manufacturing reduces labor costs and minimizes human error, leading to greater productivity and efficiency. This trend is particularly beneficial for high-volume production runs where repetition and precision are paramount.
Quality Control Techniques
Advanced quality control methodologies, such as statistical process control (SPC) and non-destructive testing (NDT), ensure that every part meets strict industry standards. This commitment to quality is essential in manufacturing sectors, especially those that prioritize safety and reliability.
Choosing the Right Lathe Turning Parts Manufacturer
Selecting the right lathe turning parts manufacturer is vital for ensuring the success of your project. Here are some factors to consider:
- Industry Experience: Look for manufacturers with a proven track record in your specific industry.
- Technological Capabilities: Ensure they have the latest machinery and software to handle your requirements.
- Quality Certifications: Seek manufacturers who adhere to international quality standards such as ISO 9001.
- Customer Reviews: Research client testimonials and case studies to gauge the manufacturer’s reliability.
Case Study: Deep Mould's Approach to Manufacturing
Deep Mould is a leading player among lathe turning parts manufacturers. Their approach emphasizes technology-driven processes combined with a customer-centric philosophy. Here are some key aspects of their operations:
Innovative Solutions
Deep Mould utilizes cutting-edge CNC technology to offer highly customized parts tailored to client specifications. This approach ensures that each component fits perfectly within the larger assembly of the machinery it is intended for.
Commitment to Quality
By implementing rigorous quality control procedures, Deep Mould guarantees that all products meet or exceed industry standards. Regular audits and testing help maintain high-quality benchmarks, resulting in zero defects in delivered components.
Customer Engagement
Deep Mould prides itself on its strong relationships with clients. They provide support from the initial design stage through to production, ensuring that all client needs and expectations are met.
Conclusively Navigating the Future of Lathe Turning
As technology continues to evolve, the role of lathe turning parts manufacturers will only become more significant. Advances in materials science, automation, and AI are set to revolutionize manufacturing processes further.
In conclusion, the contributions of lathe turning parts manufacturers to the manufacturing landscape cannot be overstated. Companies like Deep Mould exemplify excellence in the field, and understanding their significance and methodologies allows businesses to make informed decisions about their sourcing needs. By leveraging their expertise and advanced technologies, industries can ensure that they remain competitive in today's fast-paced environment. Remember, investing in quality manufacturing leads to better products, enhanced reputation, and ultimately, greater business success.